ERFOLGSGESCHICHTE EINES KUNDEN
SmartWeld+ füllt die Lücken beim Schweißen in der Produktion
Als die Experten für Produktionsautomatisierung von teamtechnik mit der Entwicklung eines Produktionsschweißsystems beauftragt wurden, wandte man sich in Sachen Laser-Knowhow an Coherent. Am Ende hat teamtechnik einen Partner gefunden, der das Unternehmen unterstützt, Kunden kontinuierlichen Support zu bieten.
Das auf Produktionsautomatisierung spezialisierte Unternehmen teamtechnik liefert alles – von manuellen bis hin zu vollautomatischen schlüsselfertigen Systemen – für Fertigung, Montage und Prüfung. Sein Fachwissen umfasst ein breites Spektrum an Technologien, einschließlich der Handhabung von Teilen, verschiedener Testmethoden und Fügeverfahren, hauptsächlich für die E-Mobilitätsindustrie. Im Jahr 2019 wurde es von einem Hersteller von Akkupacks für handgeführte Elektrowerkzeuge gebeten, ein Produktionsschweißsystem zu entwickeln.
Insbesondere wurde teamtechnik damit beauftragt, automatisierte Lösungen für das Schweißen von 11 verschiedenen Verbindungen zu liefern. Dazu gehörte das Zusammenfügen einer Vielzahl von Materialien. Da das Unternehmen kein umfangreiches Fachwissen zum Laserschweißen im eigenen Haus hatte und viele Prozesse in kurzer Zeit entwickelt werden mussten, wandte man sich für Unterstützung an Coherent Labs.
Schweißen auf intelligente Art
Das Team von Coherent wurde mit Materialproben versorgt. Eine Reihe von Tests zeigte deutlich, dass all diese Prozesse mit dem Coherent SmartWeld+ Bearbeitungskopf, gekoppelt mit einem 1 kW Singlemode-Faserlaser (dem HighLight FL1000CSM), erfolgreich durchgeführt werden können.
SmartWeld+ ist ein spezielles Schweißgerät, das eine fortschrittliche Form der Strahlformung, einschließlich einer Vielzahl von Oszillationsmustern, beinhaltet. Außerdem ermöglicht es eine präzise Kontrolle der abgegebenen Laserenergie während des Schweißvorgangs. Auf diese Weise können Breite, Tiefe und Einstichprofil der Schweißnaht sorgfältig gesteuert werden. Es ist besonders nützlich für die Verbindung hitzeempfindlicher Materialien und unterschiedlicher Materialkombinationen, wie z.B. Kupfer mit Aluminium oder Stahl. Außerdem kann es stark reflektierende oder flüchtige Materialien mit weniger Spritzern, Porosität und Rissbildung schweißen.
Schwierige Materialien
SmartWeld+ ermöglicht sogar die Verarbeitung „schwieriger” Materialien, d.h. solcher, die traditionell nicht mit dem Laserschweißen kompatibel sind. Einige der bei diesem Akkupack verwendeten Materialien fallen in diese Kategorie.
Bei einer Schweißung muss beispielsweise ein 0,5 mm dickes Stück verzinktes Kupfer mit einem 1,0 mm dicken Stück nickelbeschichtetes Kupfer verbunden werden. Der niedrige Schmelzpunkt von Zink hat in der Vergangenheit Probleme beim Laserschweißen bereitet. Insbesondere blubbert es chaotisch, wenn es auf die zum Schmelzen von Kupfer erforderliche Temperatur gebracht wird. Dies führt zu Hohlräumen und Porosität in der fertigen Schweißnaht sowie zu einer erheblichen Menge an Spritzern.
Dieses Teil musste an beiden Enden geschweißt werden. Ein Ende war flach und das andere Ende hatte eine 90°-Biegung. Diese Bedingungen waren so unterschiedlich, dass zwei separate Parametersätze entwickelt werden mussten, um jede Schweißnaht zu optimieren. Außerdem ist in das Werkstück ein Kunststoffteil eingebettet, das beim Schweißen nicht erhitzt werden darf.
Die Möglichkeit, die genaue Form der Schweißnaht mit SmartWeld+ anzupassen, war hier sehr nützlich. Sie ermöglichte die Herstellung einer Verbindung, die groß genug war, um das erforderliche Maß an elektrischer Verbindung und mechanischer Festigkeit zu gewährleisten, ohne zu nahe an das Kunststoffteil heranzukommen. Während auf beiden Seiten des Teils ähnliche Schweißbahnen verwendet werden, sind die Richtungen, in denen sie angebracht werden, unterschiedlich. Die Entwicklungsteams von teamtechnik Poland und Coherent stellten außerdem fest, dass bei einer der Schweißnähte optimale Schweißergebnisse mit einem kleinen Abstand zwischen den Teilen erzielt wurden.
Bei beiden Schweißungen war ein wichtiger Teil der Lösung die dynamische Leistungsmodulation. Dadurch wird das Schmelzbad während des Schweißens stabilisiert und Porosität vermieden. Außerdem werden Spritzer erheblich reduziert.
Umgang mit Prozessvariabilität
Bei einer weiteren Schweißung wurden zwei 0,3 mm dicke Stücke SIGMACLAD® miteinander verbunden. SIGMACLAD ist ein Verbundwerkstoff, der speziell für die Herstellung von elektrischen Verbindungen in Li-Ionen-Akkus in Packs entwickelt wurde. Es handelt sich um ein fünflagiges Sandwich, bestehend aus Ni|Edelstahl|Cu|Edelstahl|Ni. Diese Kombination bietet mehr wünschenswerte Eigenschaften als jedes einzelne Metall. Insbesondere das Kupfer sorgt für eine hervorragende elektrische und thermische Leitfähigkeit (zur Wärmeableitung), während die Edelstahlschichten das Material leichter schweißbar machen und die Festigkeit der Schweißverbindung erhöhen. Die äußeren Nickelschichten erleichtern das Löten und verleihen eine gute Korrosionsbeständigkeit.
Da SIGMACLAD speziell für die Kompatibilität mit dem Laserschweißen konzipiert wurde, erwarteten weder die Entwicklungsteams von teamtechnik noch von Coherent, dass diese Verbindung eine große Herausforderung darstellen würde. In der Praxis stellte sich jedoch heraus, dass Materialdickenschwankungen, individuelle Schichtdickenschwankungen und geringe Maßtoleranzen der Teile zu Prozessabweichungen und inkonsistenten Passungen führten. Die Tests ergaben, dass eine Fixierung erforderlich ist, um den Spalt zwischen den beiden Teilen auf weniger als 0,05 mm zu begrenzen, damit die Schweißnähte zu 100 % erfolgreich sind.
Die gesamte Schweißnaht ist in diesem Fall 1 mm x 2,5 mm. Der fokussierte Laserstrahl ist viel kleiner, so dass SmartWeld+ den Strahl mehrmals hin- und herbewegt und dabei zwischen den einzelnen Scans leicht in die senkrechte Richtung geht, um den gesamten Bereich abzudecken. Außerdem haben die Tests gezeigt, dass es notwendig war, den Laser während der Bewegung zu modulieren, da es sonst zu übermäßigen Spritzern an den Enden des Scans kam.
Einige der Prozesse änderten sich sogar noch, nachdem die Geräte in der Fabrik des Endverbrauchers installiert und in Betrieb genommen worden waren. Die Applikationsingenieure von Coherent stellen weiterhin Unterstützung bereit, um auf etwaige Maßnahmen zu reagieren.
In einer Schweißnaht wird zum Beispiel 0,3 mm dickes SIGMACLAD mit 1,0 mm dickem nickelbeschichtetem Kupfer verbunden. Das Problem trat hier erst auf, nachdem das Gerät bereits zwei Jahre lang erfolgreich vom Endbenutzer installiert und betrieben worden war. Dann änderte der Materiallieferant seine Rezeptur und es kam zu Problemen mit der Sauberkeit des Kupfers. Dies führte zu einer beträchtlichen Menge an Spritzern bei der Verwendung des Prozessrezepts, das sie ursprünglich ohne Schwierigkeiten verwendet hatten.
Die Flexibilität des SmartWeld+ erwies sich in diesem Fall als besonders wertvoll. Insbesondere die Möglichkeit, die Schweißparameter über die Software-Steuerung zu variieren, ohne Änderungen an der Hardware der Vorrichtung vornehmen zu müssen. Ein neuer Testzyklus bei Coherent ergab, dass die Modulation der Laserleistung in diesem Prozess das Problem lösen würde.
Zusammen zum Erfolg
Durch die Zusammenarbeit mit dem Entwicklungsteam von Coherent konnte sich teamtechnik auf das konzentrieren, was sie am besten können – nämlich Automatisierung. „Wir brauchten einen Partner, um all diese Laserschweißverfahren innerhalb der Zeit- und Kostenvorgaben unseres Kunden zu entwickeln”, erklärt Maciej Zaborowski, Spezialist für Schweißtechnik bei teamtechnik POLAND. „Wir wollten vor allem jemanden finden, der über das Fachwissen und die Einrichtungen verfügt, um die Materialien zu testen und festzustellen, ob sie alle mit dem Laser geschweißt werden können, und dann spezifische Prozessrezepte zu entwickeln, die in der Produktion funktionieren würden.”
„Coherent hat in all diesen Punkten geliefert. Außerdem endete unsere Zusammenarbeit mit ihnen nicht nach dieser ersten Prozessentwicklung. Sie haben uns weiterhin unterstützt, als Änderungen bei den Materialien zu Produktionsabweichungen bei Prozessen führten, die bis dahin gut funktioniert hatten. Wir konnten keinen anderen Laseranbieter finden, der dieses Maß an Prozessverantwortung übernehmen würde.”
„SmartWeld+ liefert uns großartige Ergebnisse und lässt sich problemlos an Prozessänderungen anpassen. Aber der eigentliche Grund, warum wir uns für Coherent entschieden haben, ist ihr Support. Kein anderer Anbieter war bereit, die notwendige Entwicklungsarbeit zu leisten, um sicherzustellen, dass wir die Anforderungen unserer Endkunden erfüllen können.”
— Maciej Zaborowski, Spezialist für Schweißtechnik, teamtechnik POLAND
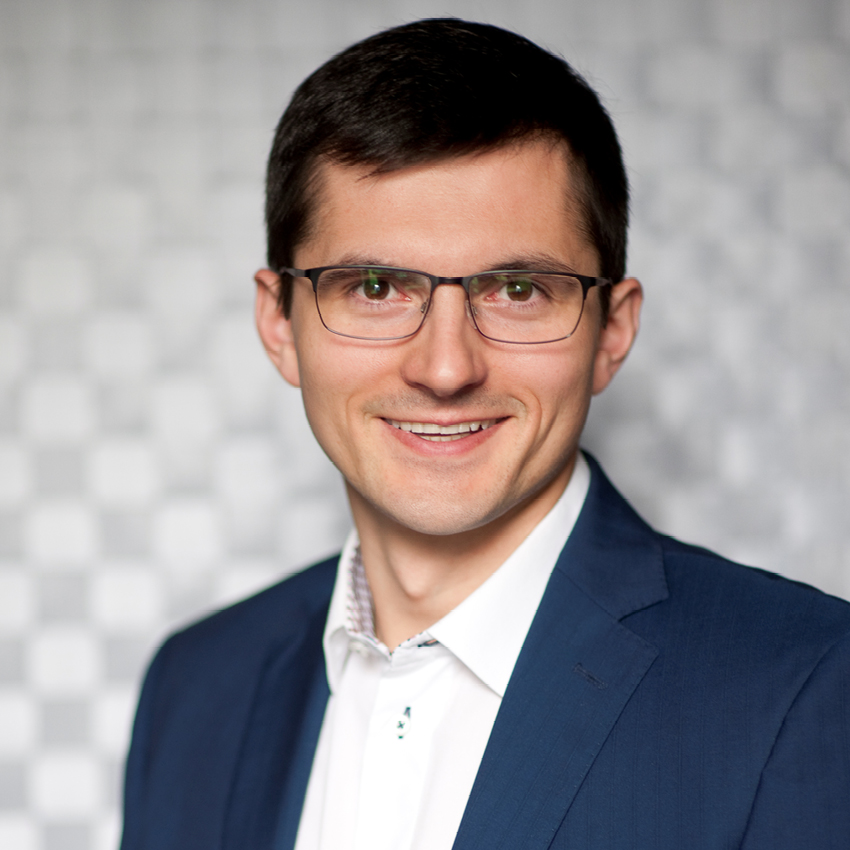
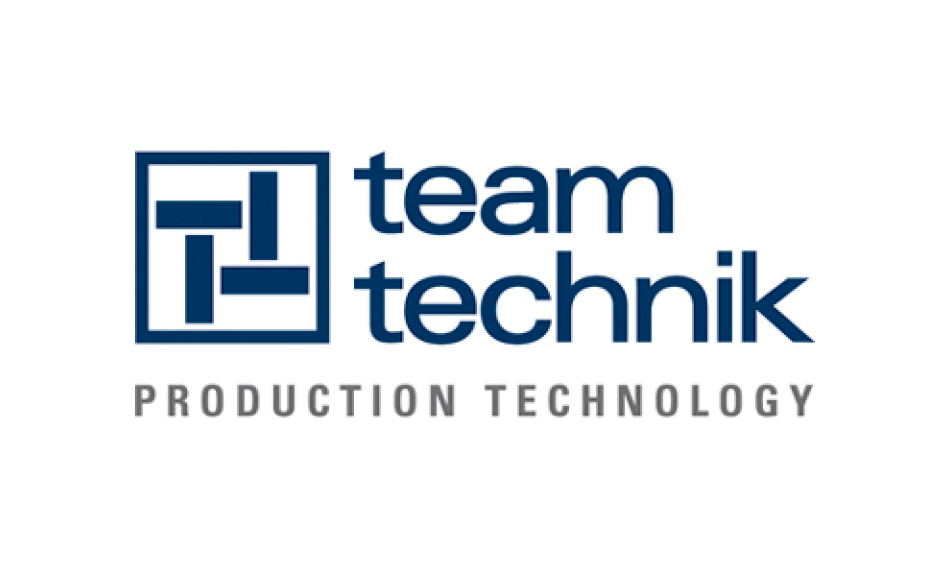
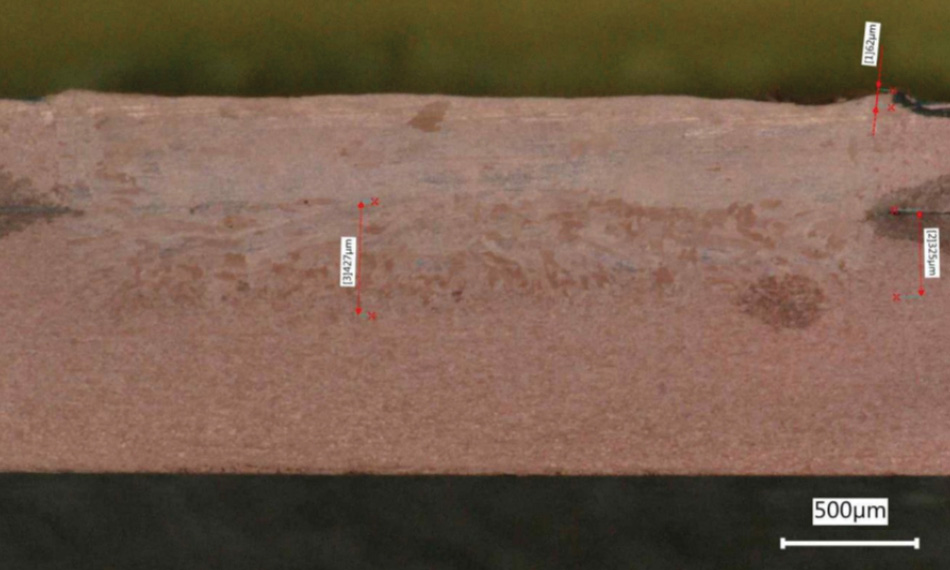
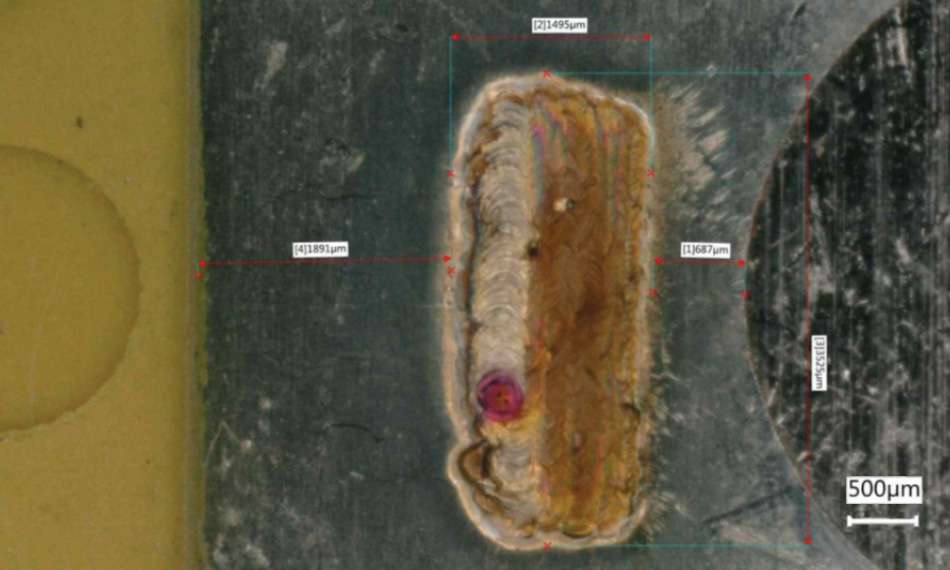
Abbildung 1. Querschnitt und Draufsicht der Schweißnaht von 0,5 mm zinkbeschichtetem Kupfer auf 1,0 mm nickelbeschichtetes Kupfer.
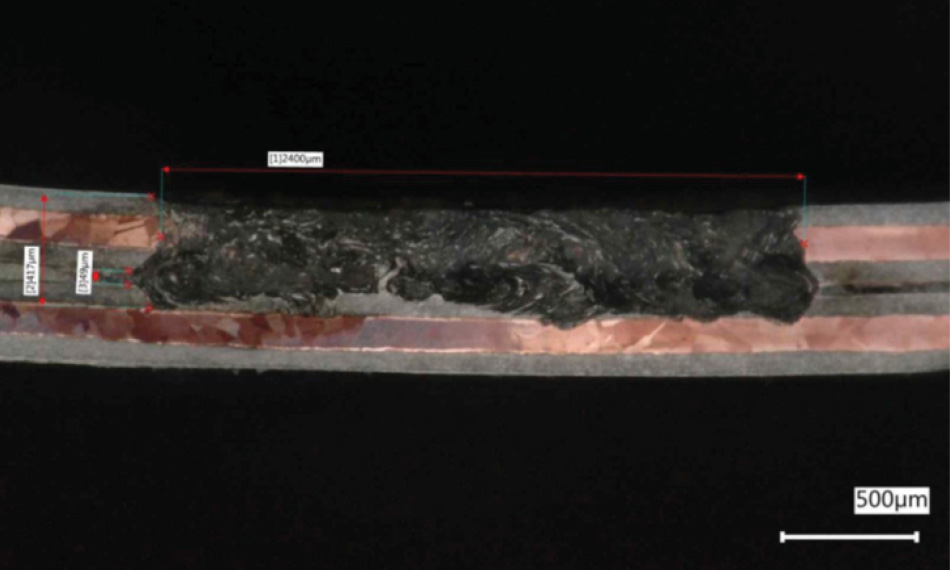
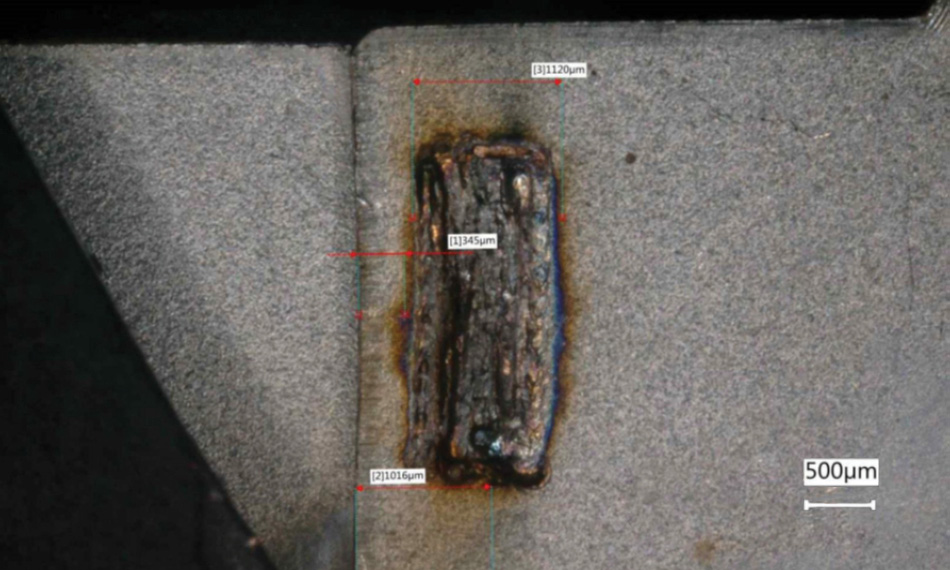
Abbildung 2. Querschnitt und Draufsicht der 3 mm SIGMACLAD auf 3 mm SIGMACLAD Schweißnaht.
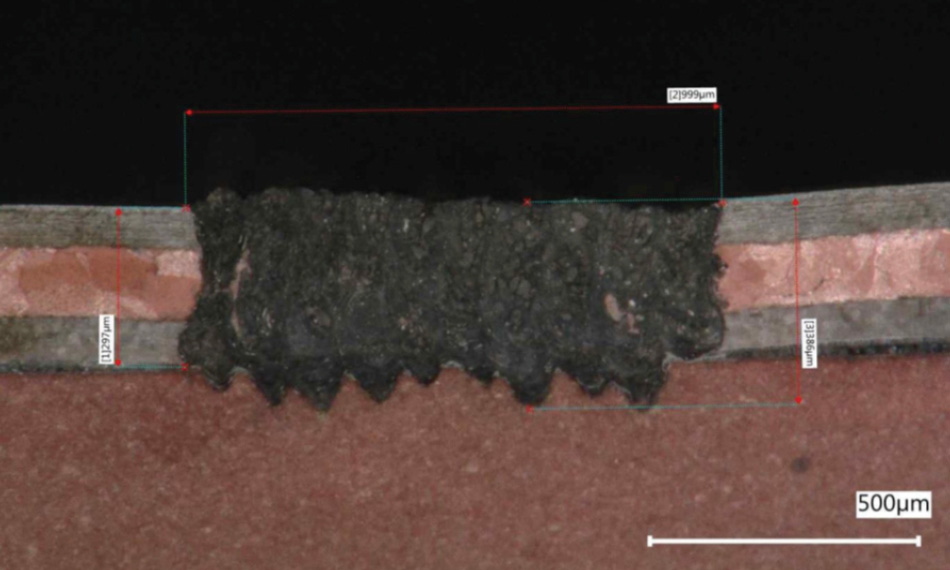
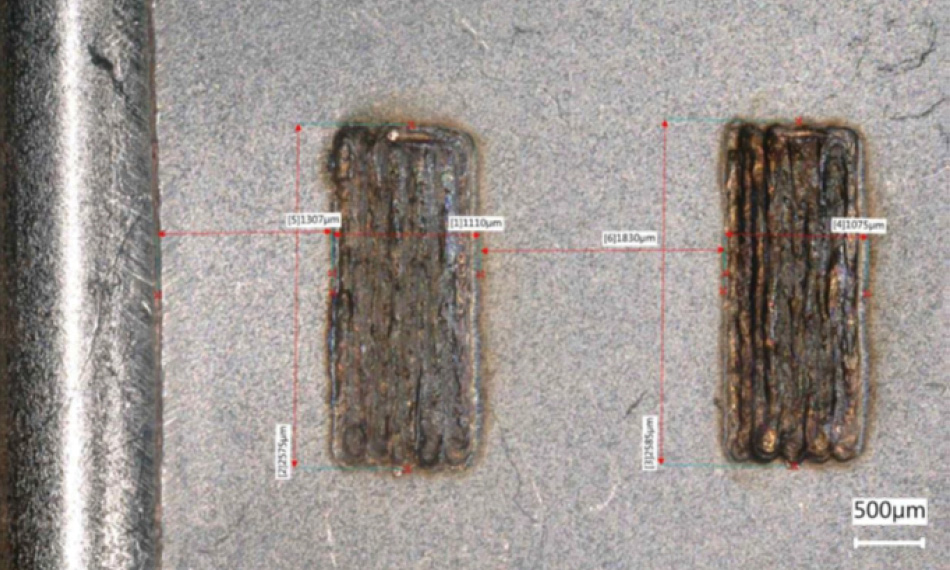
Abbildung 3. Querschnitt und Draufsicht der 3 mm SIGMACLAD auf 1,0 mm nickelbeschichtete Kupferschweißnähte.