Lasers Conduct High-Speed Busbar Stripping for EV Production
CO2 lasers efficiently strip insulation from electrical busbars, and are readily integrated into the automotive manufacturing environment.
January 27, 2022 by Coherent
As automakers gear up to make electric vehicles (EVs) in larger numbers, every aspect of how they’re produced is being refined. The goal, of course, is to lower cost while also improving vehicle reliability and performance.
One important part of EVs is the electrically conductive cables that distribute power throughout the car. These are called busbars. Because of the amount of electrical current they need to carry, busbars aren’t just wires. They’re thick, ribbon-shaped metal conductors with insulation around them (typical dimensions are in the range of 12 mm wide x 3 mm thick). The metal itself is most often copper, or sometimes aluminum. The insulation is a plastic material (usually polyamide PA12).
The insulated busbar material is often supplied in long lengths on a spool, just like a traditional wire. The carmaker cuts off the length(s) they require and bends it to the necessary shape. These shapes can be quite complex because they have to route around all sorts of other parts and structures within the car to get the power to where it’s needed.
At some point in production, some insulation has to be removed (stripped) from the two ends of the busbar. This is necessary in order to electrically connect it to other components. Auto manufacturers have a few specific requirements for this process.
First, insulation stripping has to be fast in order to be cost-effective, and not to bottleneck production. This means removing around 25 mm or so (1 inch) of insulation in just a few seconds.
Second, the insulation has to be removed completely. Because any residual insulation in the stripped area can interfere with the electrical connection, and therefore waste power (lower vehicle efficiency). Plus, the ends of the busbar are often welded to other conductors or batteries. Any plastic left on the conductor surface will contaminate the weld, which degrades its electrical and mechanical properties.
Finally, the conductor itself can’t be damaged by stripping. This could reduce its mechanical strength creating a possible point of failure.
All these reasons pretty much rule out removing the insulation using any kind of mechanical method, like a blade or scraper. Also, it’s hard to remove insulation from a curved or odd-shaped surface using a blade.
Laser busbar stripping takes off
These same requirements make lasers great tools for busbar insulation stripping. This is because the laser process is completely non-contact, and can readily be configured to work with curved parts. This makes laser processing fast and flexible.
CO2 lasers, in particular, are ideal for this task. This is because the CO2 laser produces far-infrared light. This light is very strongly absorbed by most of the plastics used for insulation, but highly reflected by the copper.
What this means is that the laser light rapidly vaporizes the insulation, but then automatically stops removing material when it reaches the conductor (because the copper just reflects the laser light back rather than absorbing it). So, it’s easy to remove the insulation, while leaving the copper totally intact.
Laser busbar stripping in production
To actually perform insulation stripping, the laser beam is focused down to a small spot on the busbar to concentrate its energy. This focused beam is rapidly scanned back and forth to cover the entire area over which insulation must be removed.
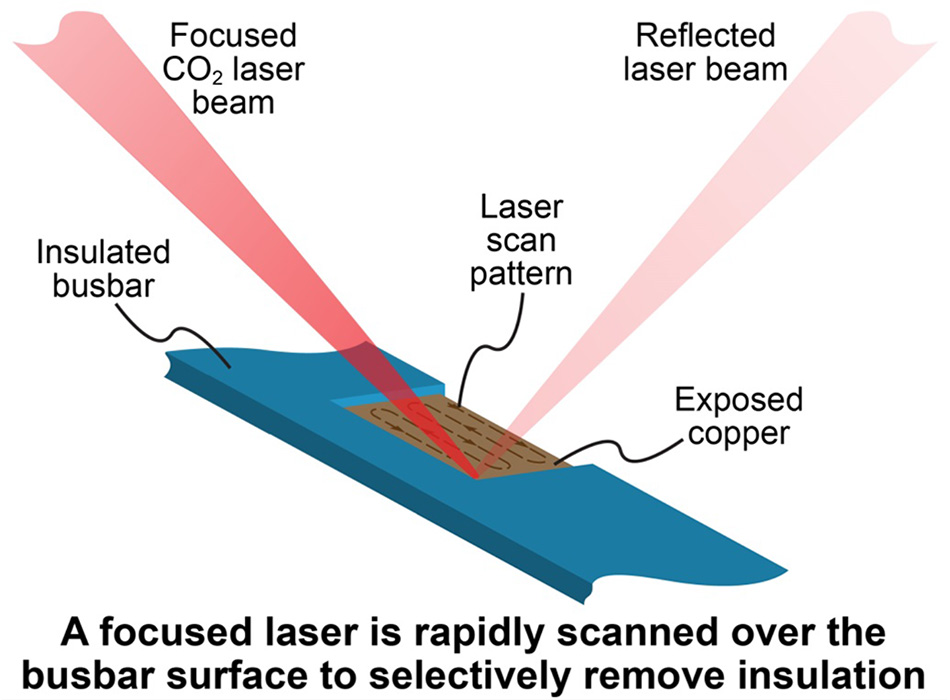
There are some important practical considerations when implementing this method in a production environment. For example, two lasers are used in order to get the necessary process throughput. Each one strips insulation from one side of the busbar (so, there would be a second laser coming from underneath in the drawing). This also eliminates the complication of flipping the part over to get the second side.
Also, it’s best to have the laser beam hit the busbar at an angle. This does two things. First, it avoids the chance that any laser light will be reflected back and damage the beam delivery system. Second, it enables the laser to remove insulation from both the top and the edge of the busbar at once (since the angled laser beam can “see” the side of the busbar).
The busbar system is a complete solution for stripping busbars. It includes two PowerLine C sub-systems, and all the associated scanning and beam delivery optics, together with all the necessary control electronics and software.
The PowerLine C can remove a 30 mm length of 0.5 mm thick polyamide from both sides of a 6 mm wide busbar in about 6 seconds. Insulation removal is complete without any damage to the conductor, delivering a high yield process.
There are two different busbar stripping systems available - an inline version and a stand-alone version. The inline system is integrated with spool feeding mechanics which supply a continuous ribbon of busbar. The laser strips this prior to cutting and a final bending operation. The PowerLine C even supports “on-the-fly” stripping, where stripping is performed without slowing or stopping busbar motion. In the stand-alone version, a robot arm picks and places precut and bent busbars into the system which are then laser stripped.
See high-speed, efficient busbar stripping in action.
Related Resources